¿Qué es el slurry seal?
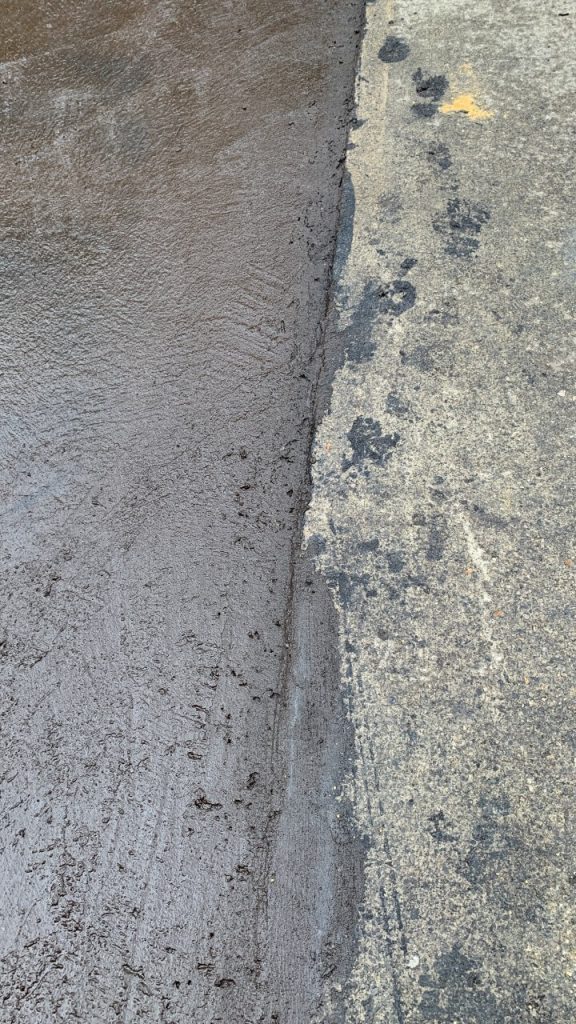
El Slurry Seal es un sello asfáltico que se aplica en superficies para solucionar una amplia gama de retos en diversos tipos de rodaduras e infraestructura vial. El pavimento slurry es una mezcla pastosa de color negro compuesta principalmente áridos, emulsión asfáltica, agua y un filler mineral.
El Slurry en algunos casos se considera como un agente rejuvenecedor del pavimento existente ya que se comporta como un inhibidor de oxidación, así como una capa de desgaste que prolonga la duración de las carreteras.
Beneficios y Ventajas del Slurry Seal
El slurry se puede aplicar prácticamente en todos los tipos de pavimentos y carreteras, bien sean flexibles o rígidos. Sus grandes ventajas han extendido su aplicación y uso desde pistas deportivas hasta autopistas que conectan países. El slurry puede ser aplicado con un enfoque de mantenimiento preventivo o bien con un fin correctivo de patologías en carreteras.
Esta lechada bituminosa no solo aumenta la estabilidad de las rodaduras al reducir y ralentizar su proceso de envejecimiento, sino que además tiene una serie de beneficios a corto y largo plazo. El primer efecto del pavimento slurry es mejorar la resistencia al deslizamiento, bien sea que es aplicado sobre un concreto que ha perdido su rugosidad o sobre una mezcla asfáltica que tiene demasiada fricción con los áridos expuestos gracias a el paso del tiempo.
Este agente rejuvenecedor puede ser aplicado sobre un asfalto oxidado con el ánimo de darle más vida útil ya que el proceso de envejecimiento del pavimento original por oxidación se verá ralentizado y el mortero asfáltico será el que absorberá la mayoría de los efectos de la intemperie y los elementos. Normalmente el slurry es utilizado para el mantenimiento de pavimentos con una aplicación posterior a la construcción de la rodadura; sin embargo, en algunas ocasiones para vías de bajos volúmenes de tránsito, el slurry es utilizado como la rodadura principal en una o más capas.
También es utilizado en casos de envejecimiento prematuro, cuando se presenta una oxidación para elementos asfálticos de un pavimento por cuestiones de calidad que pueden proceder desde la refinería hasta la producción de mezclas asfálticas, para prevenir y mitigar la oxidación de los componentes asfálticos de las mezclas asfálticas originales.
Por último, una gran ventaja proviene en la facilidad de su aplicación ya que el slurry es utilizado mediante una aplicación en frío, cosa que simplifica sustancialmente su ubicuidad, seguridad para el personal que manipula y aplica los materiales, entre otros factores.
¿Cómo se prepara el Surry Seal?
A la hora de realizar un diseño de mezcla y determinar un contenido de asfalto u áridos, lo primero que se debe determinar es el tipo de slurry (Tipo I, II o III) en función del tráfico y la granulometría seleccionada y disponible en la zona. Con los anteriores factores resueltos, se procede a realizar un diseño que consiste de la mezcla de emulsión de rotura lenta (idealmente con asfalto modificado como el PRSS-94), agregados minerales bien gradados, agua y un filler mineral que puede ser cemento portland de uso general. Es fundamental obtener una consistencia de lechada pastosa que permita ser esparcida de forma homogénea en la superficie.
Adicional a la proporción de mezcla de los materiales, es necesario realizar el ensayo de materiales correspondiente a la normativa aplicable, bien sea sobre la emulsión de asfalto, agua al material que se agrega, los áridos, el filler mineral, etc. Verificar la calidad de los materiales y medir las propiedades principales de la lechada es crucial para obtener mezclas satisfactorias y no mezclas inadecuadas.
Un asfalto modificado que componga la emulsión de asfalto, especialmente diseñado para este tipo de aplicaciones, tal como el PRSS-94, garantiza que las propiedades principales de la lechada sean óptimas. La adherencia, módulo, entre otros factores se garantizan gracias a un desempeño óptimo que da el aglomerado asfáltico.
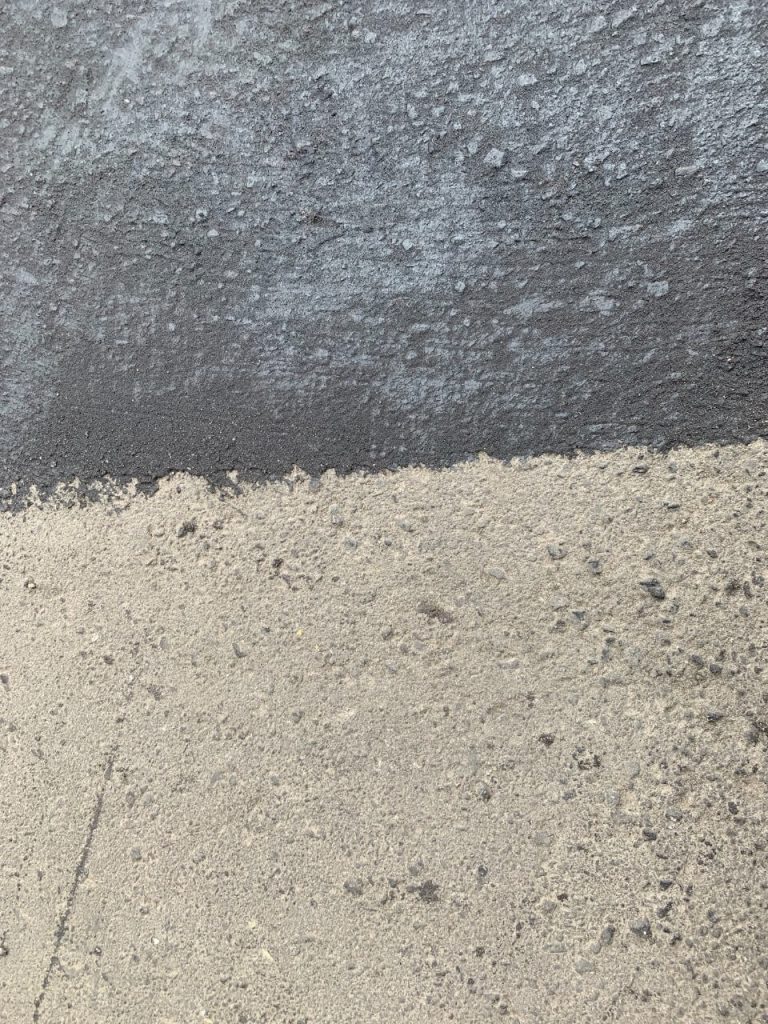
¿Cómo se aplica el slurry seal?
El slurry tiene una aplicación en frío donde la aplicación puede ser manual o mecánica, lógicamente, la aplicación recomendada para la mayoría de las superficies y geometrías es la aplicación del producto por medios mecánicos ya que se garantiza una capa uniforme y de alta calidad. Sin embargo, con una aplicación manual también es posible lograr una capa de calidad de la lechada bituminosa, teniendo controles en campo que permitan garantizar una capa homogénea.
¿Cuánto tarda en secar el slurry?
El mortero asfáltico típicamente tarda de dos a cuatro horas en secar, aunque ésto depende de factores como el tipo de emulsión, clima, temperatura, humedad, entre otros. Sin embargo, el tiempo mínimo para esperar entre capas, para slurrys que tienen más de una capa, es de 24 horas.
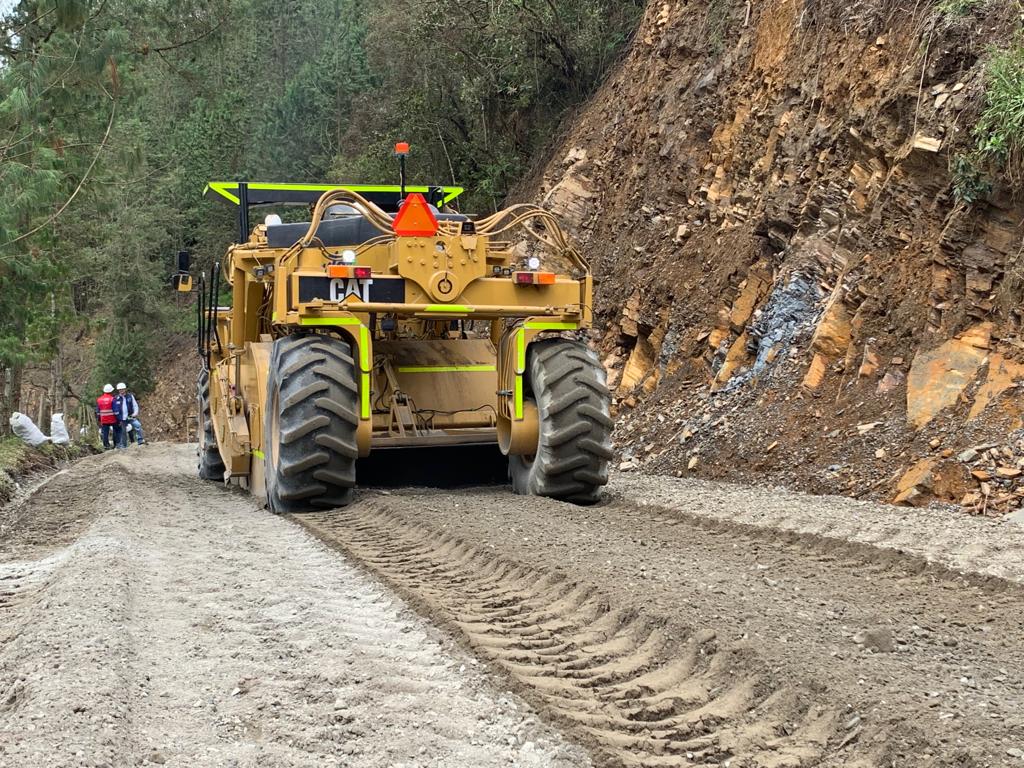