In the labyrinth of construction materials, a byproduct named fly ash takes flight toward sustainability. Once a coal combustion castaway, fly ash has emerged as a resourceful ally in construction. It speaks to a history of industrial ingenuity, transforming waste into worth.
Fly ash is not just another component; it is a testament to human innovation, redefining the properties and potential of concrete. This substance brings to the table unique characteristics that enhance the durability and reliability of our built environment. Understanding its compressive strength, bulk density, and chemical composition is crucial for builders and environmentalists alike.
By delving into the environmental implications and diverse applications of fly ash, this article aims to uncover the multifaceted benefits this material bestows upon the construction domain. From slashing carbon footprints to fortifying soil, let’s explore how fly ash is paving the way for a greener, more efficient future.
Overview of Coal Combustion Products
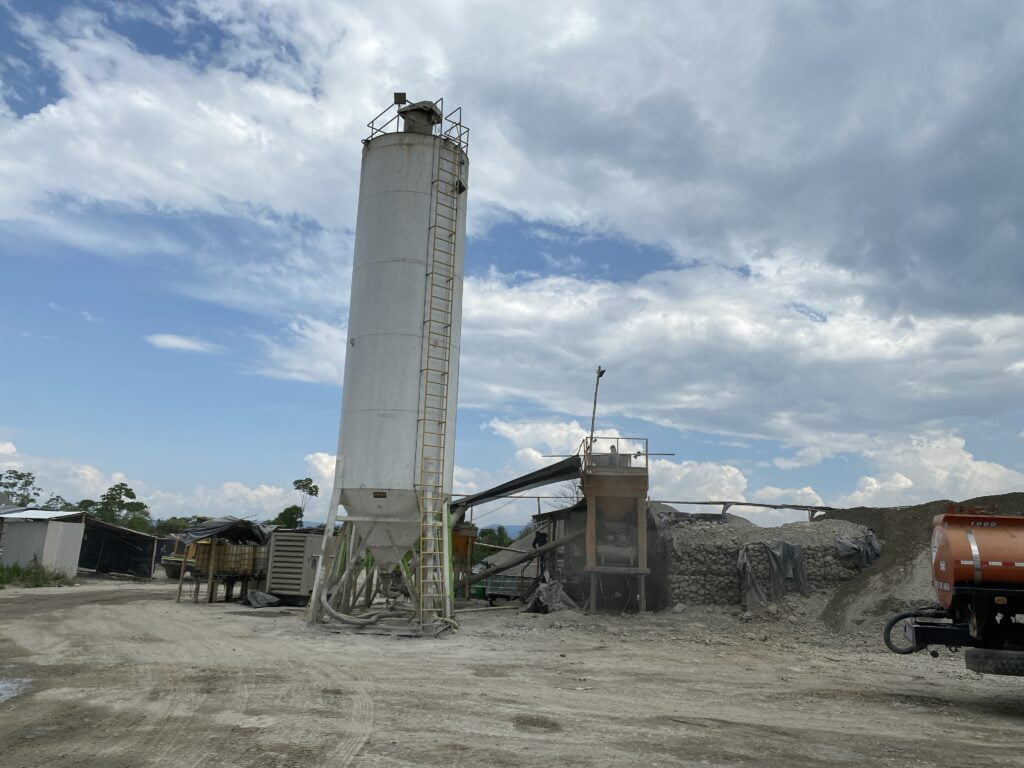
Coal Combustion Products (CCPs), also known as coal combustion residuals (CCRs), form a variety of substances generated from the combustion of coal at thermal power stations. Among these, the two prominent by-products are fly ash and bottom ash. Fly ash, a powdery material rich in silica, comes from the combustion chamber when pulverized coal is burnt. It is collected via electrostatic precipitators or other particle filtration equipment before reaching the chimney. Bottom ash, in contrast, is a coarser material that settles at the bottom of the furnace.
Another CCP is boiler slag, which ensues when molten bottom ash from specific boilers cools rapidly, resulting in black, glass-like pellets. Also categorized under CCPs is flue gas desulfurization (FGD) material, derived from procedures intended to reduce sulfur emissions. FGD material can vary in consistency from wet sludge to dry powder, containing various sulfites and sulfates.
These combustion by-products have widespread applications, including in the production of concrete bricks and for soil stabilization. Fly ash, specifically, is praised for enhancing the compressive strength and reducing the bulk density of concrete products. However, concerns over heavy metals and toxic substances—including potential radioactive elements—require careful management and use of these materials.
Properties of Fly Ash
Fly ash, an advantageous by-product of coal combustion in thermal power plants, is not merely a homogenous material but rather an intricate composite with variances in its mineral context and chemical composition. It comprises calcium-bearing minerals such as anorthite, gehlenite, akermanite, calcium silicates, and calcium aluminates, echoing constituents commonly found in Portland cement. These similarities lend fly ash its esteemed compatibility with concrete applications, as it can impart both physical and chemical enhancements.
The mercury concentration in fly ash can fluctuate, occasionally reaching levels up to 1 ppm, its exact measure dictated by the sort of coal burned, whether anthracite, bituminous, or lignite. To ensure utility, the American Society for Testing and Materials (ASTM) C618 sorts fly ash into two classifications: Class F and Class C. The categorization is primarily determined by the material’s calcium, silica, alumina, and iron content, indicating varied utilization potentials.
For it to replace cement in concrete, fly ash must meet specific benchmarks, exhibiting a fineness of 45 µm or below and a carbon content, gauged by its loss on ignition, capped at less than 4% in the United States. Physically, fly ash presents as a fine material, subtler than Portland cement and lime. Its particles are predominantly spherical and silt-sized, measuring generally from 10 to 100 microns, a property enhancing its functional contributions to building materials.
Compressive Strength of Fly Ash Concrete Bricks
Fly ash lends itself remarkably well to the production of construction bricks, with bricks containing as much as 50% Class C fly ash satisfying or even surpassing the performance criteria of traditional clay bricks as established by ASTM C 216. The compressive strength inherent to these fly ash bricks meets expectations, while also aligning with the shrinkage parameters delineated in ASTM C 55 for concrete brick.
The procedure for fabricating fly ash bricks promises not just efficacy but also sustainability, poised to reduce the embodied energy in masonry construction by up to a striking 90%. Class C fly has self-cementing characteristics, significantly bolstering the compressive strength of the resultant concrete bricks, a trait quantifiable according to ASTM D 5239. This standard probes the strength of cubes composed of fly ash and water after a dedicated curing period, offering measurable benchmarks for this material’s performance.
Bulk Density and Characteristics of Fly Ash
Fly ash’s utility in construction is greatly informed by its bulk density and specific characteristics. Typically, the density of fly ash fluctuates between 1.8 and 2.3 g/cm³, situating it at roughly two-thirds the density of Portland cement. The bulk density of this material varies as well, from 0.6 to 0.9 g/cm³, with vibrated bulk density recorded between 1.0 and 1.3 g/cm³. High calcium fly ash exhibits a marginally greater density than standard fly ash.
Particle gradation sees coarser distinctions in coarse fly ash when likened to cement, rendering it an apt substitute in mortar and other building materials, replacing aggregates without compromise. Indicators crucial to assessing fly ash’s suitability in concrete include loss on ignition (LOI), fineness, chemical makeup, and uniformity—each underscoring a distinct aspect of its integration in construction materials.
Chemical Composition of Fly Ash
The primary oxides forming the majority of fly ash’s chemical structure are silicon, aluminum, iron, and calcium. Other elements present, albeit in lesser amounts, include magnesium, potassium, sodium, titanium, and sulfur. This composition defines fly ash as a material with particles generally ranging from 10 to 100 microns in size, mostly spherical, contributing to its pozzolanic reactivity when integrated with concrete.
ASTM C618 identifies two primary classes of fly ash based on chemical content: Class F and Class C, each originating from distinct coal types and containing differing compounds. For instance, Class C, often coming from sub-bituminous coals, encompasses calcium alumino-sulfate glass, quartz, tricalcium aluminate, and unbound lime (CaO). When used as a mineral admixture in concrete, fly ash fosters the formation of cementitious compounds through a chemical reaction with cement and water, bringing forth improved properties in the hardened material.
Environmental Impact of Fly Ash
Fly ash, a byproduct of coal combustion from thermal power plants, presents a unique opportunity to improve the environmental profile of the construction industry. Using fly ash in concrete production does more than enhance durability and extend the lifespan of roads and structures. It brings a multitude of eco-friendly benefits that reduce the untoward effects of construction on the environment.
Firstly, incorporating fly ash into construction materials leads to less reliance on energy-intensive ordinary Portland cement. This shift results in considerable energy savings and in the reduction of greenhouse gases and other harmful air emissions related to cement production. Moreover, fly ash use conserves natural resources by replacing some of the raw materials required for traditional concrete. This substitution means fewer resources are extracted from the environment, lessening the ecological footprint.
Additionally, fly ash utilization in building materials significantly decreases the amount of coal combustion products relegated to landfills. By repurposing fly ash, we are diverting massive quantities of waste from landfills, thereby reducing the potential leaching of hazardous substances into the surrounding environment.
Reduction of Carbon Content in Construction Materials
A key environmental advantage of fly ash is its ability to reduce carbon dioxide emissions within the construction field. Roughly 0.9 tons of CO2 emissions are offset for each ton of fly ash used in place of traditional cement. The innovative treatment process known as Carbon Blocker® has made it viable to use even carbon-rich fly ash in cementation. This advancement is groundbreaking in minimizing the carbon footprint of construction materials.
Fly ash’s utilization makes the production of concrete more energy-efficient, improving building performance while cutting down on carbon emissions. As an added benefit, using fly ash can contribute to achieving Leadership in Energy and Environmental Design (LEED) points, which are essential for green building certification.
Mitigation of Toxic Metals in Soil Stabilization Applications
Fly ash is not just beneficial in concrete; it is also a resource in the stabilization of soils. When used in soil stabilization, fly ash improves the physical properties, such as shear strength, and helps manage the expansion and contraction behaviors of the soil due to moisture changes. This improves the soil’s capability to support structures and pavements.
Design and testing of soil stabilized with fly ash can lead to the establishment of precise mixtures that secure desired engineering properties, including the mitigation of toxic metals in the ground. This use can decrease the soil’s acidity, trapping harmful ions and thereby reducing the mobility of toxic metals like aluminum.
Furthermore, the pozzolanic reaction occurring in fly ash contributes to the sequestration of heavy metals in fly ash-based bricks (FAB). This reaction promotes higher strength and aids in the containment of metals such as Cd, Ni, Pb, and Zn, allowing FAB to be classified as a nonhazardous waste material.
Application of Fly Ash in Thermal Power Stations
Fly ash, emerging as a significant byproduct from coal-fired thermal power stations, encompasses a vast range of beneficial applications far beyond the confines of its origin. Characterized by the presence of essential plant micro- and macronutrients, fly ash presents unique physicochemical properties esoteric to the enhancement of soil systems. The strategic application of fly ash onto lands can unleash a plethora of advantages, chiefly nutrient supplementation and pH correction, alongside profound improvements to the physical conditions of the soil.
The incorporation of fly ash within concrete mixtures leads to notable enhancements in properties, elaborating workability, heightened compressive strength, diminished drying shrinkage, reduction in permeability, and elevated resistance to deleterious reactions such as alkali-silica reaction (ASR) and sulfate attack. This aligns with the ideology of sustainable construction, advocating the utilization of recycled materials to taper greenhouse gas emissions and potentially accrue LEED points pertinent to eco-friendly building assessments. Furthermore, the unique particle shape of fly ash permits a more fluid concrete mix, necessitating decreased water usage, ultimately lowering the exothermic temperature during curing and mitigating the propensity for crack formation, thereby bolstering the durability, and extending the lifespan, of constructed entities.
Use of Fly Ash in Cement Production
The use of fly ash in cement production is a vanguard of industrial symbiosis, promoting a circular economy approach within the construction sector. The manufacturing process of incorporating fly ash into cement involves mechanical air classification to perfect the fineness of the ashes and ensure the carbon content remains under the threshold of 4% to 6%, as mandated by regional regulations. This alchemy, in which fly ash is blended with concrete, forges materials of superior durability and longevity, while simultaneously offering a palpable reduction in energy consumption and greenhouse gas emissions.
Flaunting pozzolanic properties, fly ash reacts with calcium hydroxide in the aqueous realm to form newfound cementitious compounds. These compounds contribute substantially to the cementitious matrix in concrete, thereby aligning with an overarching vision of diminished environmental impact through lowered CO₂ emissions from cement manufacturing. Additionally, the inclusion of fly ash in concrete recipes tempers the thermal kinetics during curing, preventing cracks and amplifying the overall strength and resilience of the resulting material.
Utilization of Fly Ash in Soil Modification Projects
The versatility of fly ash extends to the terra firma beneath our feet, enriching the utility of soil in myriad construction endeavors. As an agent of soil stabilization, fly ash significantly advances the physical properties of the substratum, such as compressive and shearing strength. These enhancements are pivotal for soil stabilization applications, which are foundational for construction projects ranging from road bases to monumental structures.
Fly ash, laden with self-cementitious virtue, dances with water to reach a spectrum of compressive strength levels, tailored to the bespoke requirements of a diverse array of construction projects in need of stable soil bases, serviceable as backfills or embankments. The spherical profile of the ash particles lends its hand to improve workability and quenches the thirst for water in cement mixtures. This elevated level of performance, through the prism of soil modification procedures, reaffirms fly ash’s role as a champion of green construction, attenuating the greenhouse gas ballet that whirls around the traditional production of Portland cement.
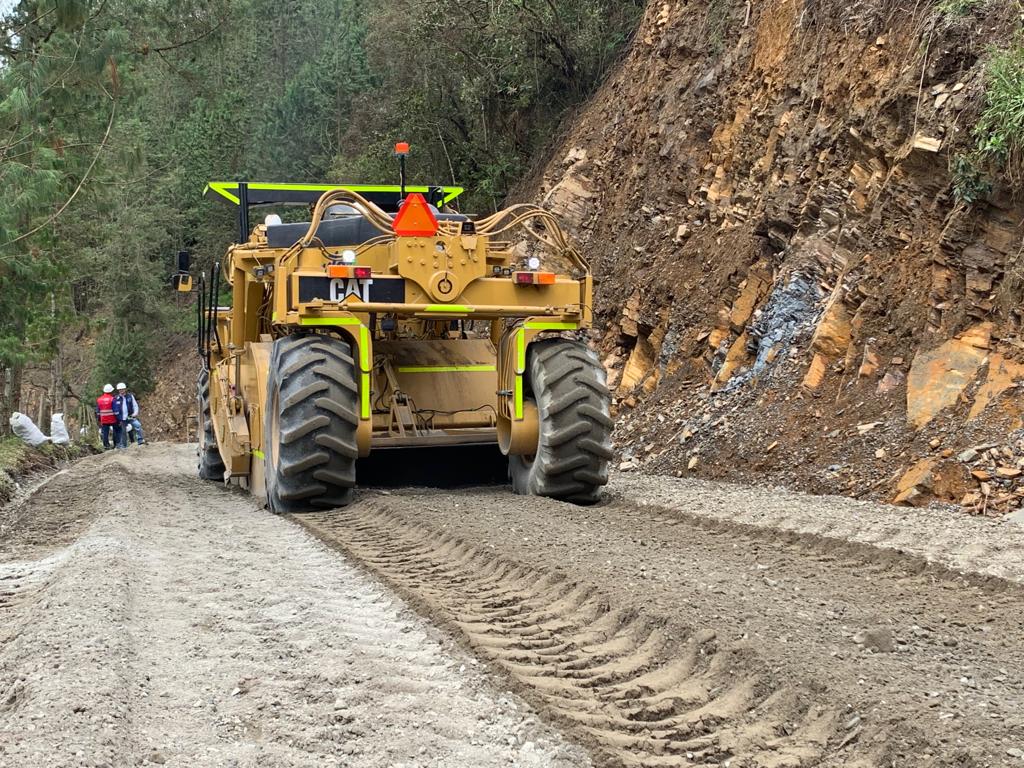
Contact us to get to work
We have a talented team, the best materials, tools, and equipment at your disposal.