Chip Seal and Bituminous Surface Treatments
Chip Seal treatments have become an ideal solution when it comes to generating a road surface for a pavement structure. This was one of the first techniques implemented in the world for asphalt paving, today becoming a viable and sustainable pavement system. These paving techniques are commonly used for pavement preservation or construction. As seen in recent years, entities all over the world using the chip seal process more and more each day. Typically these types of wearing courses, pavements or wearing surfaces consist of a liquid asphalt component blended together with an aggregate component, either crushed, sands, or crushing powders, which can be applied individually or premixed and then spread. In the case of chipseals, layers of asphalt emulsion (bitumen emulsion) are blended in layers along with crushed loose chips and sand. There are double treatments, single treatments, and triple treatments.
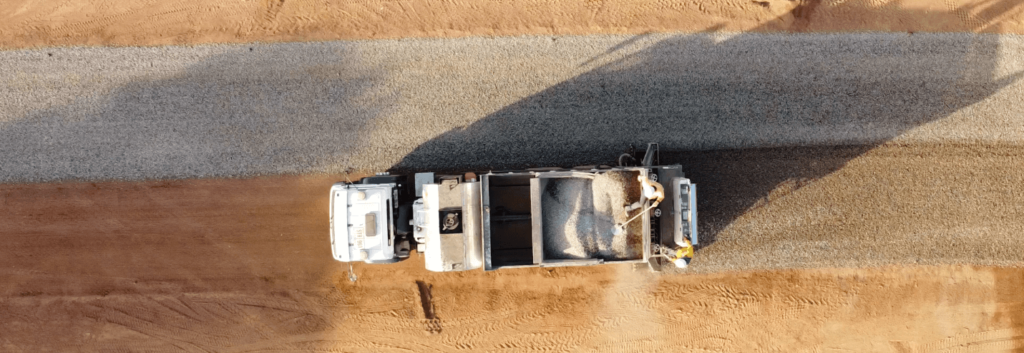
What is Chip Seal?
Chip seal is a type of pavement marking used to identify the lane boundaries of a roadway. They are typically painted onto asphalt surfaces and help drivers navigate roads safely.
The term “chip seal” refers to the fact that the surface of the pavement is cut into small pieces to form a pattern. This makes it easier for people driving over the surface to see where they’re supposed to go.
There are three types of chip seals:
• Conventional chip seal – A conventional chip seal consists of a single color design that covers the entire width of the lane.
• Striped chip seal – A striped chip seal consists of alternating rows of black and white stripes. These stripes cover half the width of the lane. Drivers can easily distinguish between the lanes by looking at the stripes.
• Multi-colored chip seal – A multi-colored chip seal consists of several colors arranged in different patterns. Some examples include red lines, yellow lines, green lines and blue lines.
What is chip sealing?
Chip sealing is done after the pavement is laid down or repaved, or even over a stabilized base course. It consists of placing asphalt emulsion onto the road surface and compressing it into place after spreading chip stones. This process creates a smooth, flat surface that is easy to maintain in any sort of weather condition. Chip sealing helps prevent water from seeping into the sub base and causing damage to the road.
Chipseals, all you need to know
In a few words, these are bituminous surface treatments that act as a protective wearing surface, the may be single, double triple, almost all three, the most common of all is the double bituminous surface treatment. This is a cost effective wearing course applied in unpaved or paved roads that is basically composed of a bituminous binder, generally applied at room temperature, although it can also be heated up to 60ºC, followed by a layer of gravel or two, depending on whether a single or double chipseal is being constructed. It can be implemented in a grat variety of traffic volumes.
The asphalt binder is essential in this type of surfacing as it is the product that allows the aggregates to adhere to the surface layer of the pavement surface, whether it is a base layer, paved surfaces or a stabilized soil layer, in short, to its preceding layer.
The main characteristics and benefits of chipseals, are:
- Savings in transport
- Extension of service life
- No structural contribution
- Improve the level of service and pavement life
- Protect the pavement structure from the elements
- Provide a safe ride for vehicles
- Reduce traffic noise
- Minimal surface level increase
- Asphalt appearance at a fraction of the cost
Amongst the different types of chipseals and asphalt pavement surfaces, we at Pro-Road specialize in the following cost effective solutions:
- Single Chipseal / Surface Treatment
- Double Chipseal (Double bituminous surface treatment)
- Triple Chipseal / Surface Treatment
- Fog Seal
- Microsurfacing
The term “chipseal” refers to a type of pavement marking material that consists of asphalt mixed with small pieces of stone or gravel. This mixture is applied to the road surface and spread evenly over it.
Chipseals are usually applied to unpaved surfaces such as dirt roads, parking lots, and airport runways. These materials cost less than resurfaced concrete or asphalt concrete pavements, but they do not last nearly as long.
There are several types of chipseals. One common type is known as “tarseal.” Tarseals consist of asphalt mixed with crushed rock and sand. Another type of chipseal is known as “chip,” which includes asphalt and aggregate. A third type of chipseal contains both asphalt and aggregate.
The chip sealing process
Chip sealing is used to make roads watertight. First, a layer of gravel is laid down on the road surface. Then, an emulsion mixture is applied to the road surface. When it dries, the gravel forms a hard shell over the emulsion. This prevents moisture from penetrating the road surface.
A layer of gravel is placed over the emulsified surface. The gravel particles are smaller than those found in normal road construction. They allow water to pass through the road surface while keeping larger stones out.
After the emulsion dries completely, workers use a vibrating machine to compact the gravel into the road surface. This helps ensure even distribution of the gravel throughout the road.
Single Chip Seal / Single Bituminous Surface Treatment
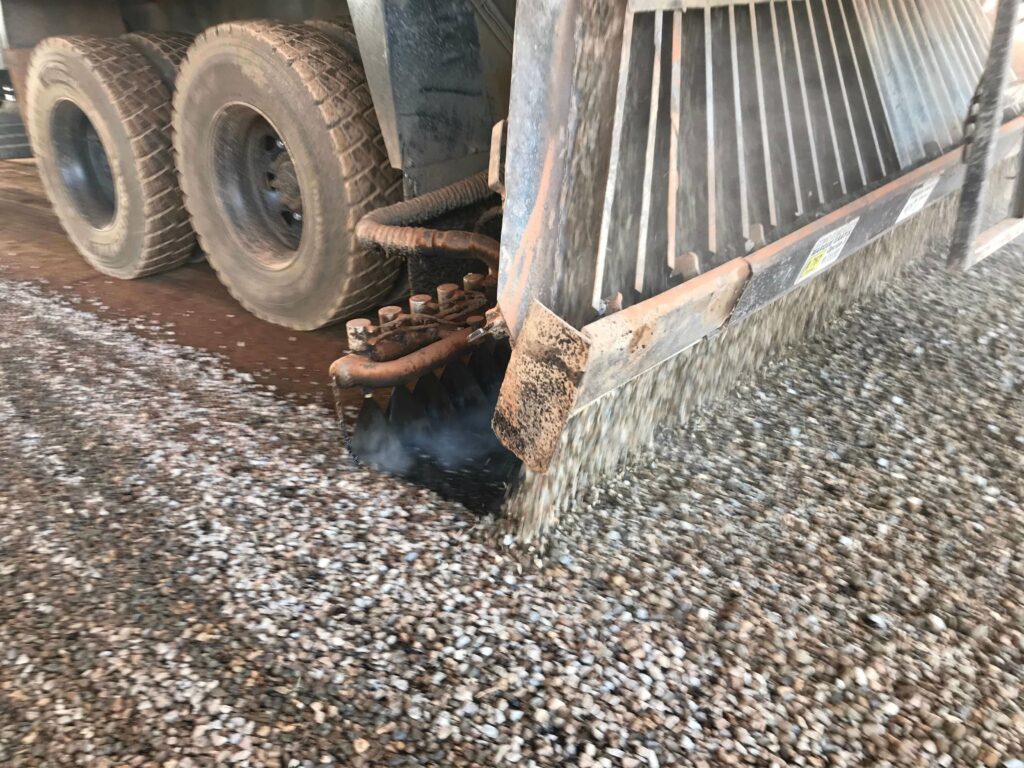
The single chipseal or Monolayer treatment consists of an asphalt overlay of asphalt emulsions, ideally polymer-modified, such as PRIM-18, followed by a layer of gravel/shredded and then compacted. For these simple treatments, the first step is the application of asphalt over the surface of the road structure, either granular or stabilized soil, followed by the application of aggregate and its compaction. It is possible that prior to the asphalt emulsion layer, there is a light application of asphalt cement in the form of an emulsion, ideally with a slow emulsion to improve the adherence of the wearing course to the surface and not to apply directly the modified emulsion of the surface treatment. It is important that the aggregates to be used comply with a series of characteristics of wear, size (homogeneity), and also in their shape (fractured faces). It is important to pay special attention to the emulsion dosage since too little emulsion can result in the detachment of the aggregates from the surface and too much emulsion can result in bleeding of the surface. Sometimes simple treatments are followed by a final layer of asphalt binder followed by a layer of sand. It is essential to verify compliance with requirements for full compliance as this is a single application layer. It is recommended that manuals such as Chipsealing in New Zealand (Transit New Zealand) or Low Volume Road Design Engineering (Robert Douglas) be consulted for this purpose.
¿What is a Double Chip Seal / Double Bituminous Surface Treatment?
A Double Bituminous Surface Treatment, also known as Double Surface Treatment, Double Chip Seal, consists of multiple applications consisting of a layer of asphalt emulsion, ideally polymer-modified, such as Pro-Road PRIM-18, followed by a layer of gravel/crush and then compacted. On top of this layer is another layer of virtually the same, only with the aggregate/crush/gravel of a smaller size. It is possible that prior to the first layer of asphalt emulsion, there is a primer layer applied with a slow-setting emulsion in order to improve the adherence of the road surface to the surface, which must be applied after the first primer layer emulsion sets. It is important that the binder chosen is ideal for building a sustainable and durable pavement, and it is of vital attention to consider its characteristics, viscosity, and adherence, among other factors of the binder used. The objective of using smaller gravel in the second layer is to allow for the interlocking of the second layer within the first layer so that the pavement will have a better matrix/modulus and thus, better performance. These materials must comply with a series of characteristics of performance, size, wear, among others, and must comply with the design rate application during the chip seal application in order to avoid excess chips and bleeding from excess bitumen in double emulsions or even in single emulsions, for which the distributor truck must be carefully calibrated.
This wearing course is a “sandwich” between a layer of asphalt, followed by a layer of gravel, then another layer of asphalt, and finally a layer of gravel, smaller than the first. A surface layer of sand and a bituminous binder can also be added on top of the last layer of aggregate. This last layer tends to be applied to have better curing and to save work for the bituminous binder at the time of rising/setting, and also to reduce the voids of the last layer of aggregate by obtaining a thin surface layer on top of the last layer of aggregate. Sometimes a final layer of asphalt binder is added to the double bituminous treatments, followed by a layer of sand.
How is a chip seal applied? How is a bitumen surface treatment applied?
The construction and spreading techniques for these double treatments can vary depending on several factors; mainly in developing countries and remote areas, which is where this type of solution becomes more attractive; what determines the form of application is the available technology and the accessibility of the same to the area of the works, which also define the form of execution of treatments, or the budget, or the need to carry out the works manually to generate social inclusion. Surface treatments can be applied in various ways, from the most automated with synchronized irrigation equipment such as Romanelli or Etnyre to the most manual with labor-intensive techniques. To learn more about the different application techniques, follow the video at the end of this article.

There are details to take into account at the time of the execution of the work to cover the pavement structure. A fundamental item, which is often overlooked, is to verify that the conditioned surface is clean, swept, and free of dust to ensure optimum adhesion of the binder to the pavement structure to be sealed. The conditioned surface is the first step to making any type of surface treatment. In case the surface has a high content of fines, a slow emulsion primer can be applied. It is important to consider factors such as the height of the truck, the type of distributor truck, or if it is going to be a manual application of the chosen binder; in short, the important thing is to control the rate of application of binder per m2. Likewise, it is essential to control the gravel on the truck, and its capacity to flow; if it is going to be applied manually, the thickness of the aggregate layer must also be controlled so that it is not too thick (detachment) or too thin (bleeding). Each piece of equipment must be analyzed, the operation of the equipment to be used must be controlled by the truck driver or the primer operator, and everything must be under control to ensure that the result is a viable and durable pavement.
Regardless of how this bituminous pavement is executed, the first thing to do is to make a pavement design that guarantees optimum performance and durability. Some of the elements to be considered for the design are the chosen binder, the form of material applications (equipment to be used), the equipment available for material distribution, whether with conventional, high-tech, or manual equipment, the road traffic, and the type of material to be paved. The design of the surface treatment or pavement design must also take into account the minimum average size of the aggregates to be used; this is the factor that mainly defines the amount of binder foreseen per m2 in such a way that it is possible to stain the aggregates with enough binder so that their adherence is optimal (approximately 2/3 of their height). At the end of the pavement design, the application of asphalt per m2 or unit area is established for each underlying layer in such a way that a workable pavement results.
It is important that the aggregates to be used comply with a series of characteristics of wear, size (homogeneity), and also in their shape (fractured faces). It is important to pay special attention to the emulsion dosage since too little emulsion can result in the detachment of the aggregates from the wearing course, and an excess of the emulsion can result in bleeding of the surface.
Consultation of manuals such as Chipsealing in New Zealand (Transit New Zealand) or Low Volume Road Design Engineering (Robert Douglas) and the Minessota Seal Coat Handbook is recommended for this purpose.
Compared to asphalt pavement structures, a TSD performs better structurally on roads up to 1,000,000 equivalent axles (ESAL). Hot asphalt mixtures tend to present deformations by traction and fatigue, which is presented in pathologies such as rutting and cracking, among others, as a result of their thickness and their way of working. In contrast, deformations and compressive stresses govern the Double Surface Treatments (TSD), given its conformation, thickness, and way of working. Therefore, the TSD solutions become an economically and technically viable alternative for the vast majority of unpaved roads, especially roads with low and medium traffic volumes.
¿What’s the importance of the preseal preparation before a chip seal?
A slow emulsion primer can also be applied to the existing surface for a simple treatment or simple application of the binder to improve the adhesion of the wearing course. This thin layer of binder is applied as a pre-coat to the first layer of the TSD, i.e. its top layer, and then the first layer of aggregate is applied. This thin layer is typically used to prime bases or materials that do not end in a smooth surface such as a stabilization, for example. Since it is not a smooth surface, it is necessary to apply this type of product to compensate for the low viscosity of the asphalt surface to ensure good adhesion to the existing surface.
This double surface treatment, we can see that it can be composed of multiple layers, variable in form and technique, depending on the conditions of implementation and other variables. The multiple layers that compose it, whether for a single layer (single treatment) or composite (double treatment), require special care in all its components; from the execution of the treatment, the objective of the treatment (duration and traffic), to the application of the aggregate, the application of the asphalt, and that there is an application in proportion, since each aggregate size requires a specific application rate of bituminous binder per m2. The aggregate application must also be controlled, as well as the asphalt application rate per m2, if the aggregate application per m2 is too high, there may be pathologies of detachment, if the aggregate application is too low, there may be pathologies of bleeding. On the other hand, if the application of asphalt is too high, there may be bleeding, and on the other hand, if the application of asphalt is too low, there may be a phenomenon of detachment. Therefore, it is essential to ensure a complete application of both components to guarantee the quality of the final product.
Triple Chip Seal / Triple Bituminous Surface Treatment
A Triple Bituminous Surface Treatment (Triple Chip Seal) consists of a Double Surface Treatment but on top of it a final layer of emulsion (ideally modified or polymer enhanced like PRIM-18) is added at a lower dosage to avoid bleeding, followed by a layer of coarse sand or grit, even mixed with <4mm crushed material, and thus it is possible to obtain a third layer, better curing and a better matrix with fewer voids; in essence, the third layer of emulsion is sought that reinforces the last layer of gravel and also fills its voids to improve the matrix and also the rolling modulus.
Microsurfacing
Microsurfacing consists of a blend of controlled-rupture asphalt emulsion, ideally modified or enhanced with polymers, together with aggregates of a certain size and a filler, such as rock dust, lime and/or cement. The emulsions can be enhanced with polymers such as latex, styrene or other additives of an acrylic nature, depending on the technical requirements of the pavement. These types of solutions are also known as Micro-Surfacing, or micro-surfacing, where they can also be used on conventional pavements to extend their service life. It is important to analyze the type of asphalt technology that best suits the road needs of each project.
At Pro-Road, we manufacture and supply the best asphalt products for your chipsealing and bituminous surface treatment projects; call us.
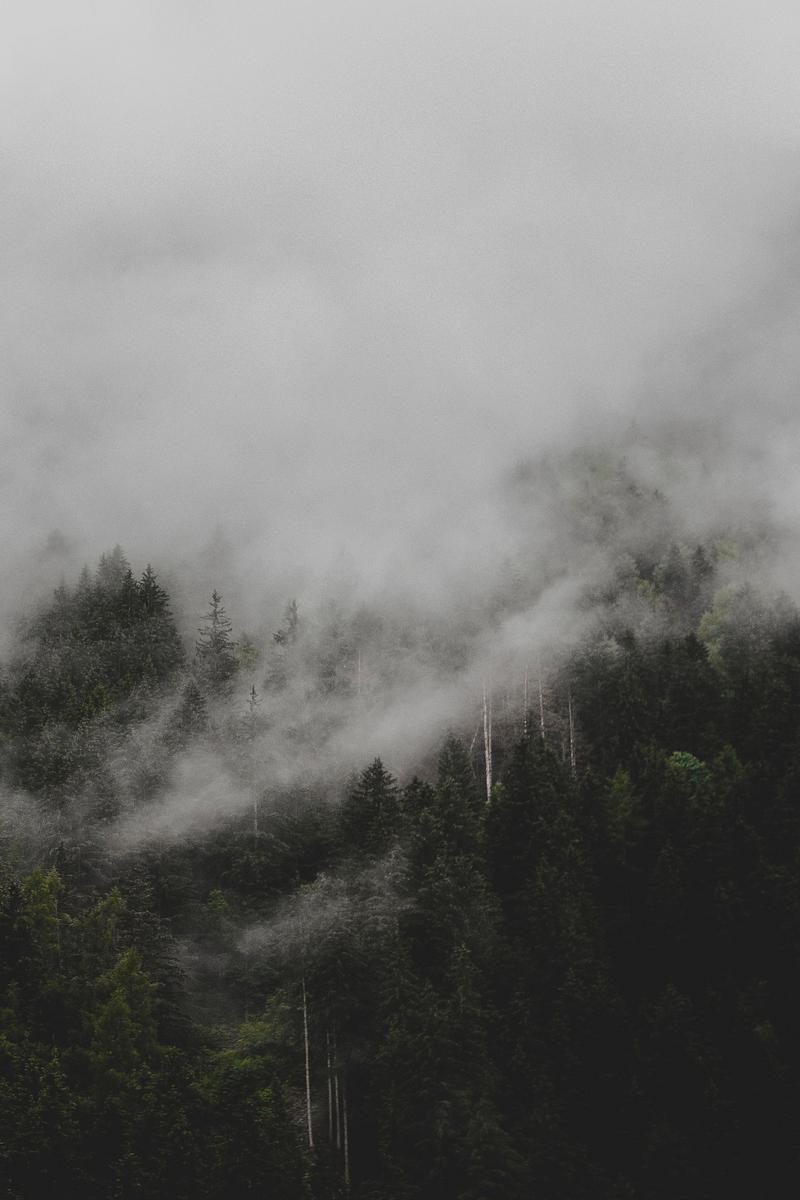